Developing a Performance and Monitoring Condition Dashboard for Bradken
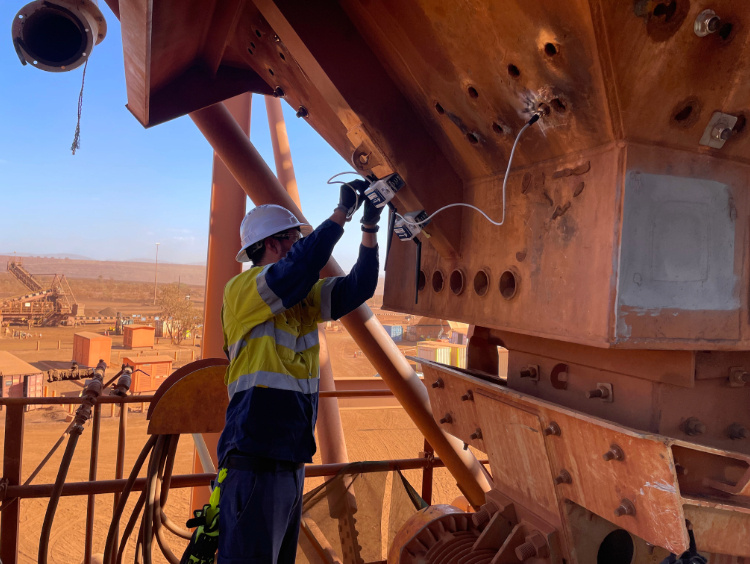
Challenge
Key to the success of its hardware monitoring solution, Bradken required a partner application and digital dashboard to capture and present data to customers, ultimately delivering a safer remote monitoring solution.
Outcome
In close collaboration, we designed and developed an interactive digital dashboard – Bradken Insite – to synchronise with the company’s SmartLiner wireless wear monitoring hardware products. With multiple releases in play, the team oversaw all timelines and deliverables to ensure smooth delivery outcomes.
Bradken equips the resource sector to sustainably advance society. Delivering an optimised future through innovative solutions to help solve its customers’ problems, it strives to improve customer operating costs and production levels through effective wear parts, services and solutions across the mining value chain.
Bradken is a wholly owned subsidiary of Hitachi Construction Machinery.
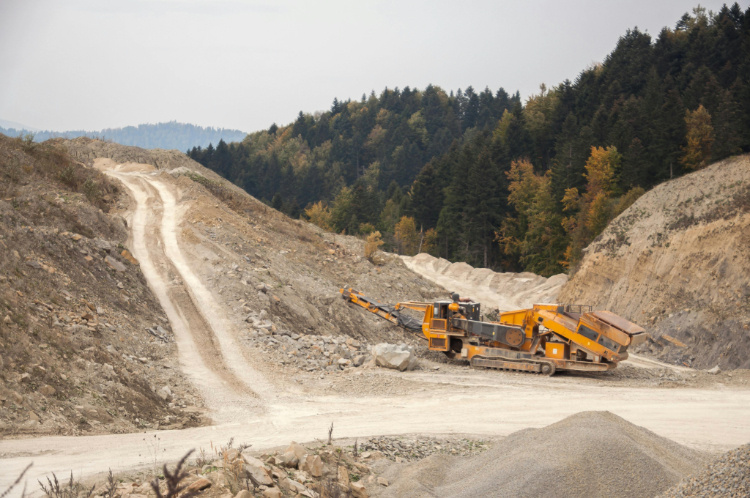
Leveraging data for safer solutions
In a sector focused on improving safety with digitisation and automation of processes, Bradken delivers wear equipment aimed at reducing product downtime and increasing machinery maintenance cycles, while improving onsite safety, efficiencies and success for its customers.
Key to the success of its hardware monitoring solution, Bradken required a partner application and digital dashboard to capture and present data to customers, ultimately delivering a safer remote monitoring solution.
The organisation sought:
- An updated digital software solution to deliver insights of wireless monitoring hardware
- Improved customer support showcasing the supply chain and financial impact avoided through wireless wear monitoring
- A solution that communicated the ease of use and power of automation
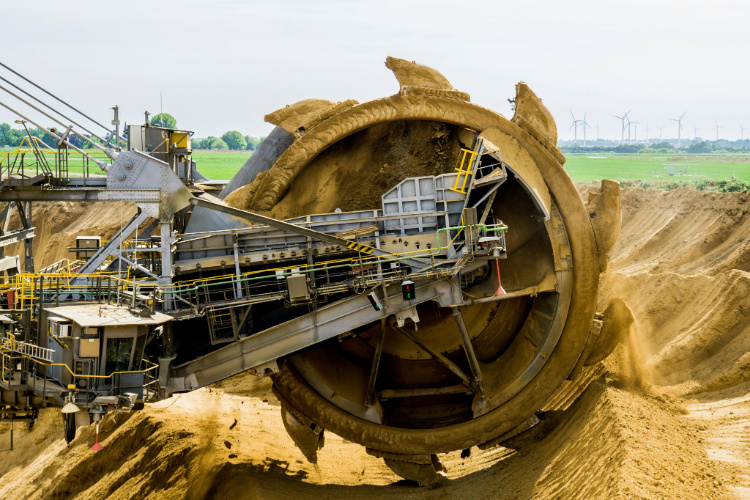
Developing a digital dashboard
Our teams supported Bradken to design and develop an interactive digital dashboard, named Bradken Insite, which synchronises with the company’s SmartLiner wireless wear monitoring hardware products.
Our UX specialists worked with key Bradken stakeholders to understand user needs and develop product roadmaps and outcomes. Developers architected a complex web app that delivered predictive graphing, 3D modelling, data capture tools and automated dashboard summaries.
We implemented a squad model to support internal Bradken teams, providing subject matter expertise and development teams to ensure a smooth roll-out of the final product. With multiple releases in play, our Project Manager oversaw all timelines and deliverables to ensure smooth delivery outcomes.
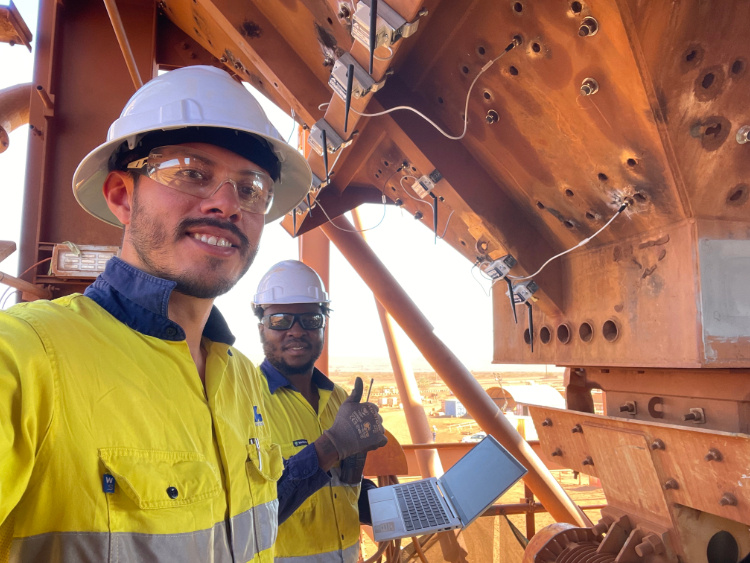
Using 3D modelling tools to map hardware data, the solution also provided an accurate visual representation wear across hardware and the ability to schedule wear data updates. It also allows for the automation of materials bills generation.
The finished product enables users to:
- Monitor and receive insights into wear and tear patterns of their Bradken equipment
- Schedule maintenance and predict downtime for particular Bradken products
- Reduce risk of downtime in an automated, highly competitive, revenue-driven industry
We were proud to be a part of the project that has improved insights into monitoring efficiencies, supply chain resourcing, safety measures and waste management.
Explore the industry
Energy and Resources
Pivot to meet the opportunities and challenges of the evolving technology landscape, with innovative, smart solutions that deliver lasting benefits.
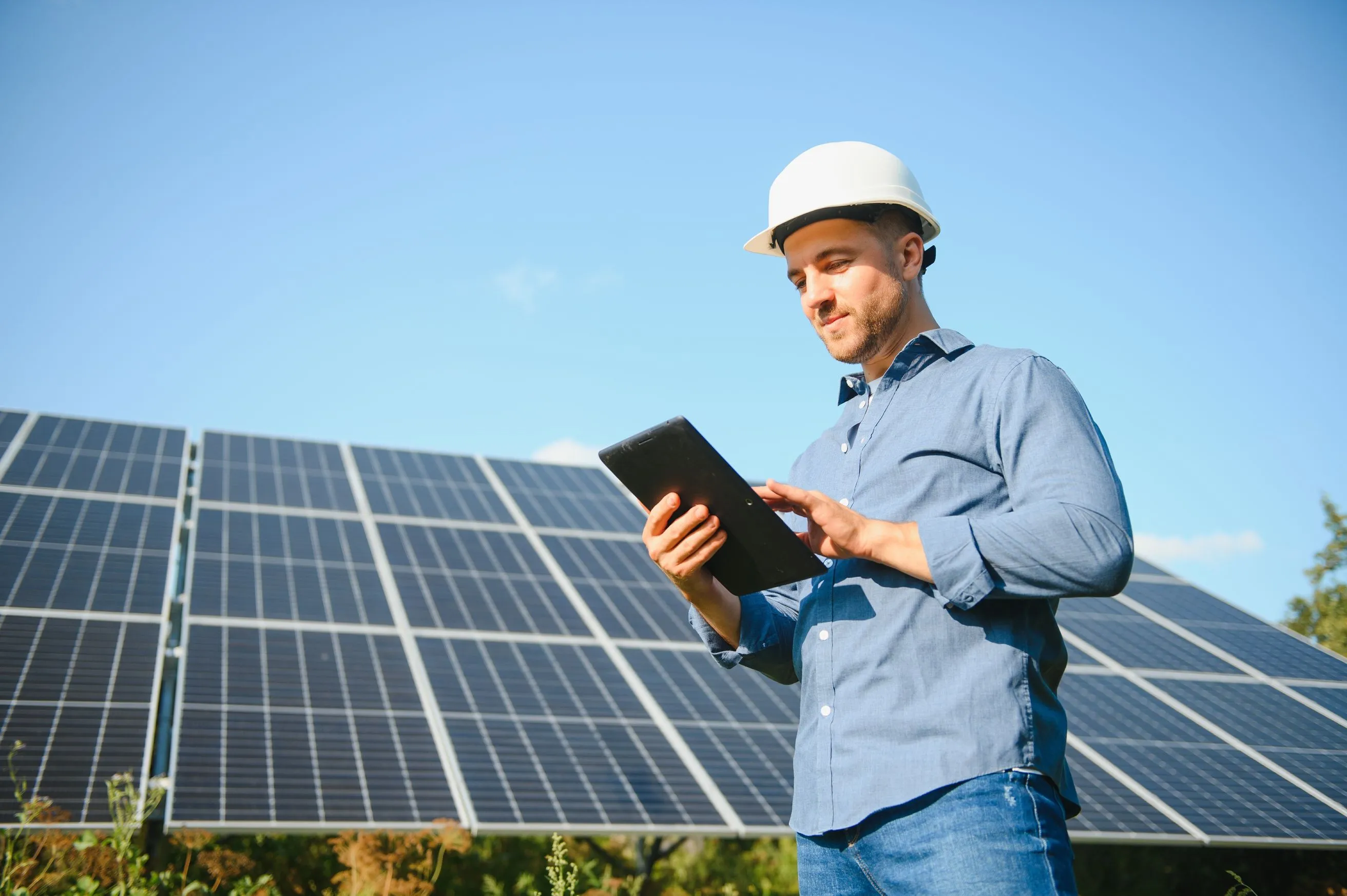