Research, Requirements and Vendor Selection for a Digital Inspections App
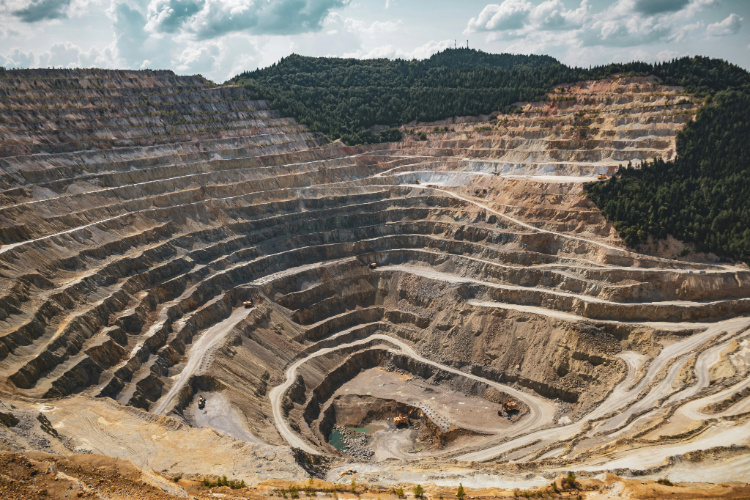
Challenge
The client, one of the world’s largest mining companies, operates 17 mines in Australia. Each had varying levels of sophistication in how it conducted in-field inspections, and there was no integration with key systems. It sought a digital solution to streamline the process.
Outcome
We supported the mining company by developing requirements for a Digital Inspection App to streamline in-field inspections. After gathering and validating requirements, we facilitated vendor selection to help find the best provider for implementation.
One of the world’s largest miners, this client sought a partner to help it develop requirements for a digital solution for in-field digital inspections.
With a need for cross-functional thinking, technological expertise and deep industry knowledge, the client turned to Endava for support
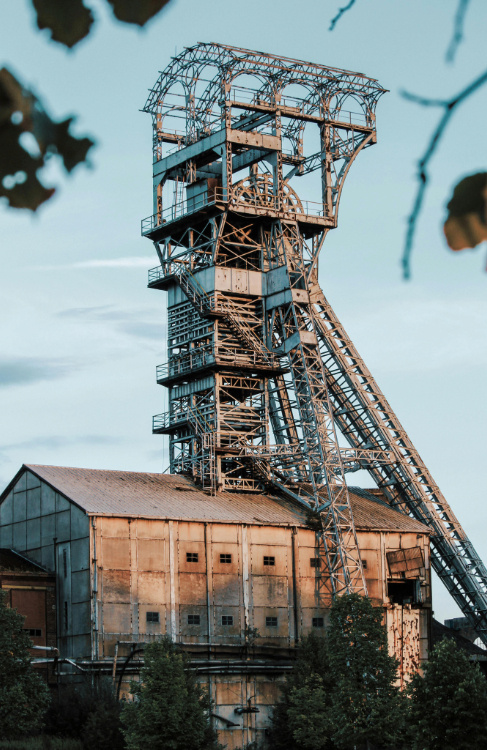
Streamlining processes across multiple sites
Operating 17 mines in Australia, this client found that each mine had a different level of sophistication in its method for conducting in-field inspections. Whether paper-based or digital forms, there was no integration back to the client’s Tier 1 and Tier 2 corporate systems.
Different systems in place at every site and department meant the organisation was facing large management and support overheads. Paper-based forms were often lost or damaged in harsh outdoor conditions, and these were time-consuming to complete.
Those who completed paper forms were then expected to input that data into Systems, Applications and Products (SAP) or CMO Compliance software, which led to inefficiencies. Errors were also more likely due to a reliance on calendars or memory for inspection schedules.
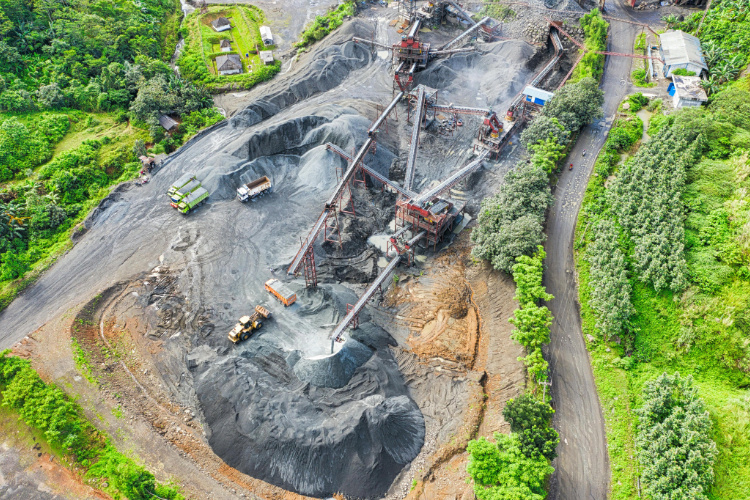
Digital app-based solution
Working in close collaboration with the client, we developed requirements for a Digital Inspection App. This mobile tool was designed to enable staff to check assets and environmental conditions and ensure they meet regulations. With this app, staff could easily access, fill out, and send digital inspection forms to reviewers and approvers.
After requirements production, we then facilitated vendor selection.
Validated personas and requirements captured early on
- Used these requirements to assess vendors objectively when demonstrating products
- Collated scoring to inform our vendor recommendation
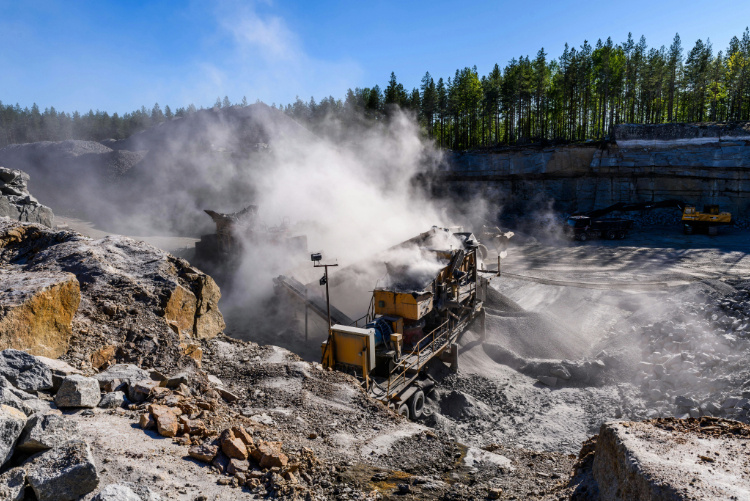
Together, we validated, created and prioritised 73 requirements both functional and non-functional, which formed the basis of a vendor assessment tool.
We then used this tool to objectively score the vendors across two 90-minute demonstrations each.
This allowed the mining organisation to confidently select a vendor and proceed with clear requirements for this app, driving efficiency and streamlining processes across its 17 sites.
Explore the industry
Energy and Resources
Pivot to meet the opportunities and challenges of the evolving technology landscape, with innovative, smart solutions that deliver lasting benefits.
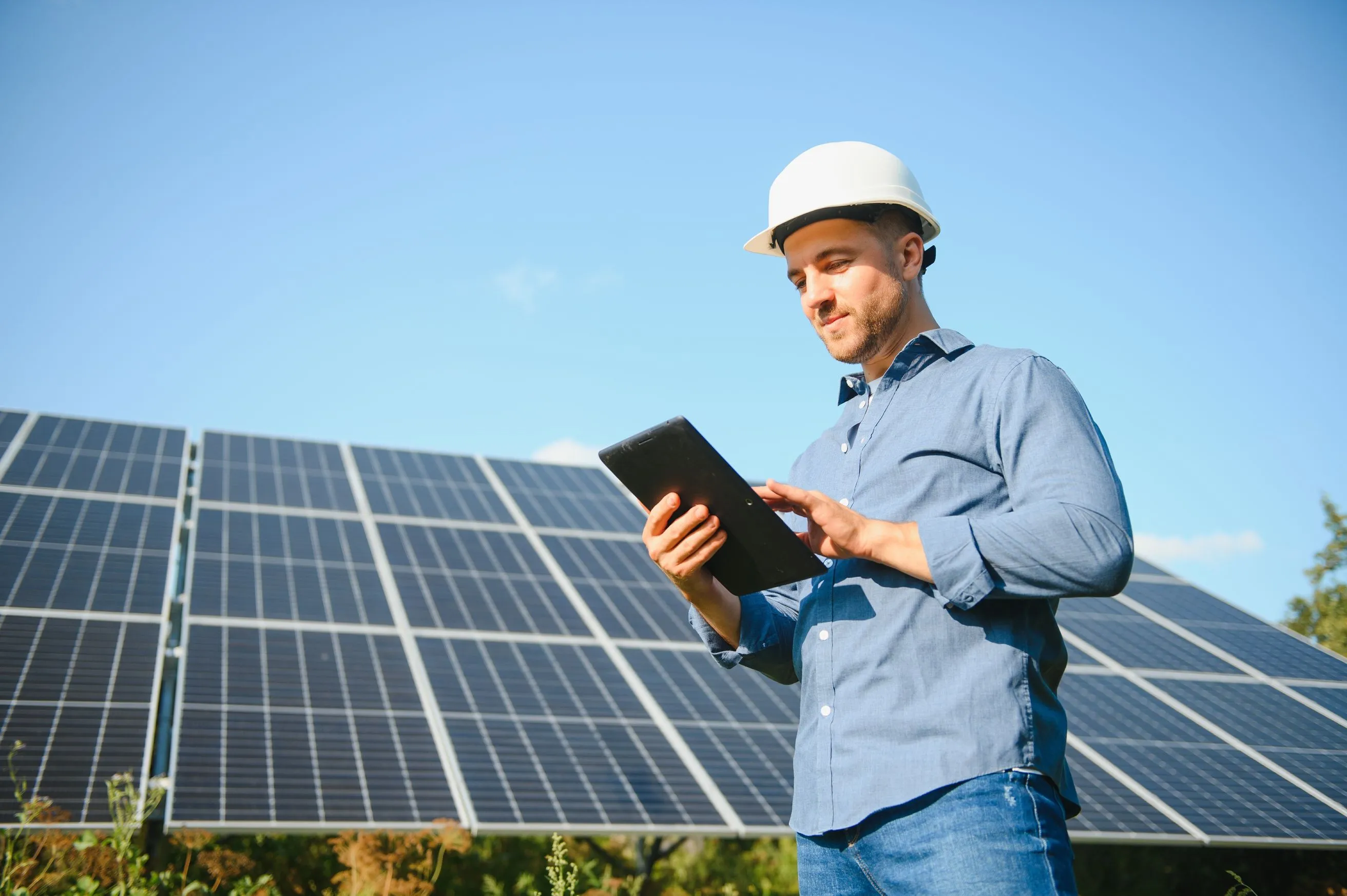
Interesting? We love when people share.